Start improving with Life QI today
Full access to all Life QI features and a support team excited to help you. Quality improvement has never been easier.
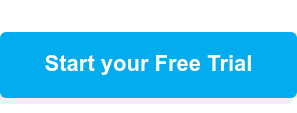
Organisation already using Life QI?
Sign-up
Statistical Process Control or SPC as it is commonly known can be daunting and can appear complex at times! We wanted to create a bit of a buzz around SPC and ask some of our Life QI users to share what they consider in their experience to be the "Top Benefits of using SPC".
Here we go!
SPC is essential in measurement for improvement! By analyzing your data through SPC you get an overview of the variation in your process. Giving you an essence of status. Do we have a problem? How big is it?
Through SPC we can interpret development in an improvement project over time and act on it. Are things going as we want? Can we identify an improvement? Through systematic measurement we can document the health service we actually provide. Allowing for full transparency for our patients.
The statistical data can explain very complex stories.
SPC helps predict future performance.
Stops people reacting negatively to peaks and troughs without just reason.
Shewhart SPC Charts are the only way to distinguish between random variation (common cause) and attributable (special) causes. Knowing which your dealing with guides how you will act and enables you to avoid tampering.
Seeing the data over time helps us to understand the behaviour in the process and, through statistical rules, know whether our change results in improvement.
Easier to understand the data behaviour in a quick way.
The SPC charts allow us to visualize special causes when they happen (outliers and trends, for example), making process assessment less subjective.
As the SPC charts are dynamic - that is, they take into account the data's history - they help in the process of decision making.
Contrary to its name, the SPC process doesn’t actually ‘control’ a process but allows the user to understand a process and act accordingly. Unlike the statistical methods used in medical research, it is the simplicity of use of the SPC process with the application of a few basic rules, which makes it ideal for quality improvement work. This is not to imply that the underlying statistical rules of the SPC process are simple. To fully understand the SPC process is to fully understand the system to which the SPC process is being applied.
Humans are visual beings and the SPC charts provide a visual interpretation of a system and the changes being applied to it. It is the ‘front window display’ for the complex data collection and analytical work that happens in the backrooms and hence is only as good as the data used.
Reducing variation is essential to providing a quality healthcare system. The SPC process allows clinicians and managers alike to understand variation within a system and respond appropriately.
The SPC process provides the critical evidence on how a system is performing however it needs a compelling narrative to connect to people and influence change behaviour.
We appreciate the above feedback from everyone involved, it is invaluable to hear from people who are frequently involved in Quality Improvement and able to sharing their experience of using SPC to record their data.
Full access to all Life QI features and a support team excited to help you. Quality improvement has never been easier.
Organisation already using Life QI?
Sign-up