Start improving with Life QI today
Full access to all Life QI features and a support team excited to help you. Quality improvement has never been easier.
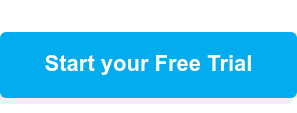
Organisation already using Life QI?
Sign-up
In this blog, we are going to look at the Virginia Mason Production System (VMPS) and its influence on Quality Improvement (QI) across the globe.
The Virginia Mason Production System is a Lean management methodology created by the Virginia Mason Institute. Its goal is to provide the ‘perfect patient experience’, to be quality leaders in healthcare and to help healthcare organisations support continuous improvement.
You can trace the roots of the VMPS back to the Virginia Mason Medical Centre in Seattle. As a high performing healthcare organisation, the leadership team was keen to further improve the quality of care and to enhance patient safety.
After having visited Japan in 2001 to learn more about the Toyota Production System, the leadership team began to develop the Virginia Mason Production System (VMPS).
The VM Institute now teaches the VMPS to healthcare leaders across the globe in order to improve patient quality and safety via a range of Lean methods. The Virginia Mason Production System is all about reducing the burden of work on team members while prompting leaders to start improvement work by asking ‘What do you think?”
The Virginia Mason Production System puts patients first and aims to promote a Lean culture within organisations. The system is all about shifting towards a culture of quality.
Celeste Derheimer is a ‘sensei’ or expert at the Virginia Mason Institute. She says: ‘Every time a leader engages the people who do the work in conversation and listens rather than coming up with solutions — or even better — asks great questions, the leader is helping to shift the culture just a little bit.’
Let’s see in more detail how the system works and the benefits the VMPS can bring to healthcare organisations.
Described by the VM Institute as a ‘long-term philosophy — a complex socio-technical system that has shaped our culture to one relentlessly focused on high quality, zero defects, exceptional service, innovation and respect for people,’ the VMPS is built on the belief that organisations will improve quality and safety for patients by eliminating waste.
‘Sources of waste are identified and eliminated over time through value stream mapping and other techniques. In essence, the VMPS focuses on defining, observing and critiquing existing care processes, setting and measuring targets, developing and experimenting with improved processes; and implementing them.’
The VMPS has strategies that range from testing and implementing small-scale ideas quickly, to planning processes further ahead and uses a range of methodologies and tools.
The VMPS philosophy is formed of five key tenets:
The Virginia Mason Production System encourages all employees who use the method to become empowered and to be ‘quality and safety inspectors’. It encourages ‘hands-on exercises to enable participants to deepen their Lean learning, refine their skills and build the capacity to teach, coach and mentor others in the tools and methods of a Lean management system.’
As well as employees, patients and their families are essential to the success of the Virginia Mason Production System, and they are regularly consulted about their experiences via interviews, questionnaires and listening sessions. The VM Institute also has a ‘Respect for People’ initiative which helps to counter disrespect among workers.
There are a huge range of benefits from using the Virginia Mason Production System. Celeste Derheimer of the VM Institute sets out: ‘This philosophy and methodology has a focus on respectful leadership, concepts and tools that work and an emphasis that the patient comes first. There’s a positive shift in attitude every time a person is shown respect, every time a person is asked, “How do you think we can improve the process?”
The benefits are such that NHS Improvement has created a five-year partnership with Virginia Mason Institute and five NHS trusts to help them to develop a ‘lean’ culture of continuous improvement which puts patients first.
Take a look at the webpage and the video to find out how VMPS is helping these trusts provide the right services at the right time and producing remarkable results. It is also ‘improving safety and clinical outcomes and patient experience and staff satisfaction while saving money.’
The Surrey and Sussex Healthcare NHS Trust (SASH) developed their clinical leadership model with the Virginia Mason Institute in 2015. This led to the trust being awarded an Outstanding rating by the Care Quality Commission (CQC).
The VM Institute also facilitates onsite Rapid Process Improvement Workshops (RPIW), which are a five-day workshop focusing on empowering people to eliminate waste and reduce the burden of work for a particular process. These workshops are designed around the plan-do-study-act (PDSA) method, and offer organisations an insight into their QI potential.
Celeste Derheimer explains: ‘Some may start out with an attitude of ‘why am I here’ but: That’s what makes this lean work so valuable. Before getting together as a team, people assume that if they do their job well, then their colleagues who are part of a process later in the patient’s care will be fine. But when they get together for the RPIW, they see how their work has a strong impact on their colleagues’ work down the line.”
Thinking about investigating the Virginia Mason Production System at your organisation? Find out more about the Institute and the methodology in further detail. Also, look at the case studies of the 5 NHS trusts involved in the partnership.
To finish with the inspiring words of Donna Smith, MD, President, Franciscan Medical Group and Senior Vice President, Virginia Mason Franciscan Health, “we have the courage to be inspired by zero defects. We have the courage to try things and learn from failure and the courage to use a method that allows the people who know the work best to be truly heard and contribute to improving work in a way that others might not be able to.”
Full access to all Life QI features and a support team excited to help you. Quality improvement has never been easier.
Organisation already using Life QI?
Sign-up