Start improving with Life QI today
Full access to all Life QI features and a support team excited to help you. Quality improvement has never been easier.
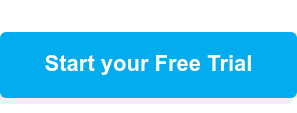
Organisation already using Life QI?
Sign-up
In past articles in this series of blogs, we have looked at Statistical Process Control (SPC) and how it works within the Quality Improvement (QI) setting. We know that SPC charts are designed to measure how a process or system changes over time.
We’re going to look in a bit more detail about how SPC charts identify the difference between positive or negative variation as well as normal and unusual variation in the data. We’re also going to show you the specific types of variation that can exist within an SPC chart, namely: common cause and special cause variation.
Just to reiterate, SPC charts – also known as control charts – are ‘decision-making tools that provide information for timely decisions concerning recently produced products’. They enable you to monitor and review the progress of QI projects and to look at trends or variation.
SPC charts have an average or mean line, and two control lines which sit above and below the average line. This enables a greater depth of statistical interpretation.
SPC charts also show individual data points, which allows more granularity. You can also use them alongside PDSA cycles – which you may well be familiar with from your QI work.
The Institute for Healthcare Improvement (IHI) recommends the visual display of data as the best way to learn from variation in QI, saying: ‘For improvement efforts, visual displays of data are often the best approach to learn from variation in data. Images are usually easy and quick to prepare, and they make it possible to access nearly all kinds of potential insight from the data.’
Let’s take a look at the variations we can monitor in our SPC charts: common cause and special cause variation.
In Quality Improvement, teams consistently use data. Both to learn from the processes they are carrying out and to predict future performance. 'Quality improvement requires using data to learn and to predict future performance. In improvement, it is critical to understand that every process has inherent variation that we want to understand.'
When you are looking at your SPC chart, you should be on the look out for two types of variation: common cause and special cause variation.
Common cause variation is something that is to be expected within your project. ‘Variation that is expected and natural in the system. Whilst this does not indicate that the system is working well, it does mean that the system is stable and predictable’. Common cause variation will always be present and is intrinsic to the whole process.
Here’s how the NHS Institute for Innovation and Improvement's document 'Guide to creating and interpreting run and control charts’ describes the common cause variation.
Common cause variation:
Special cause variation stems from external sources and control. This type of variation is not expected and therefore not a consistent part of the process. Special cause variation demonstrates that the process is out of statistical control. They show that while ‘the causes can be often infrequent, they can result in a chaotic problem. The cause could possibly be a defect in the system or a problem that has never happened before.’
Here’s how the NHS Institute for Innovation and Improvement's document 'Guide to creating and interpreting run and control charts’ describes the common cause variation.
Special cause variation:
When you note a special cause, you shouldn't implement PDSA cycles, as it shows that the system is not stable.
We’ve taken a look at common and special cause variation, but you may well be wondering what you should do when you encounter either type of variation within your QI project? Let’s take a look.
NHS England and Improvement's SPC document explains that it is normal for a process to demonstrate no cause of special variation, and therefore recommends that when you identify common cause variation, you should change the underlying process itself rather than reacting to individual performance changes. This would lead to more variation. By reducing variation you can improve your processes.
The NHS Institute for Innovation and Improvement recommends that if your process is demonstrating special cause variation, you should look into the origin of the cause. They add that: ‘changing the underlying process on the basis of special causes is a waste of resources.’
The East London NHS Foundation Trust (ELFT) use Life QI and have an excellent guide to interpreting SPC charts. The team recommends taking the following steps when you note special cause variation:
Now let’s take a look at rules pertaining to special and common cause variation, and explore the terms you might well have heard in your QI journey.
This can take place in a SPC or control chart: ‘a shift in its most basic form is eight points in a row either above or below the centerline.’
A trend is six points in a row in an upward direction or in a downward direction.
‘The use of a shift or a trend is that when seen, it is a ‘smoking gun’ for an area of improvement. The team is really hoping to see a trend or a shift because if a process always stays in the state of statistical control, the opportunity of reducing assignable-cause variation is far more challenging then if assignable-cause variation is evident.’
This is when two out of three points in the outer third of the chart, between the +2 and +3 sigma or between the -2 and -3 sigma limits.
An outlier occurs when there is a single data point above the upper control limit (UCL) or below the lower control limit (LCL).
In this article we’ve had a really good look at variation in SPC charts. As we have seen before, if you are using a software solution such as Life QI, this can make life easier for you and your QI team to interpret and act on your SPC charts to deliver better results.
To finish with the words of NHS England and Improvement's SPC document. ‘There are four rules to interpret SPC charts and if you use specialist software, these rules will be flagged so you don’t need to remember them. If one of the rules has been broken, this means that special cause variation exists in the system and once identified, can be removed.’
Full access to all Life QI features and a support team excited to help you. Quality improvement has never been easier.
Organisation already using Life QI?
Sign-up