Start improving with Life QI today
Full access to all Life QI features and a support team excited to help you. Quality improvement has never been easier.
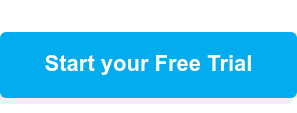
Organisation already using Life QI?
Sign-up
In this blog we are going to be taking a look at Kaizen - a quality improvement (QI) method invented by Masaaki Imai - and a systematic approach for continuous improvement in business. In his 1980s book ‘Kaizen: The Key to Japan's Competitive Success,’ Imai introduced the concept and to this day it is an important quality methodology used across healthcare and other industries. To use Masaki Imai’s own words “When applied to the workplace Kaizen means continuing improvement involving everyone – managers and workers alike."
The word ‘Kaizen’ is made up of two Japanese words: ‘kai’ means ‘to take apart’ and ‘zen’ means ‘to make good.’ When the two words are put together, it literally means taking something apart to make it better. Kaizen is also the basis of the Lean methodology, which is based on the idea of using quick cycles of learning such as the PDSA (Plan, Do, Study Act) cycle.
In the book ‘Kaizen Workshop for Lean Healthcare’ the authors promote the use of Lean methodologies to boost productivity and encourage innovation among workers, rather than using a ‘top down’ approach led by management.
The Kaizen Institute sets out the five fundamental Kaizen principles, which are:
The institute emphasises the importance of these five principles for achieving success in continuous improvement and highlights that – using these methods will ‘mark a turning point in the progression of quality, productivity, and labour-management relations.’ We will look in more details at the principles shortly.
Masaaki Imai set up the Kaizen Institute in 1985, and it continues to this day, spreading the word about Kaizen across the globe.
We’ve looked at the key 5 principles of Kaizen – now let’s take a look at the expanded 10 principles of Kaizen, which form the core of the philosophy and methodology:
These principles are there to help guide you on your Kaizen journey and keep you focused on what’s really important in your quality improvement journey.
Described as ‘part action plan and part philosophy’, Kaizen promotes the thinking that the smallest of ideas can create great results. Kaizen encourages continuous improvement cycles to achieve continuous improvement, using a number of tools and approaches to achieve success such as value stream mapping, Total Quality Management and other technologies.
Let’s take a look at the two areas of Kaizen and how they work together:
‘As an action plan, Kaizen is about organizing events focused on improving specific areas within the company. These events involve teams of employees at all levels, with an especially strong emphasis on involving plant floor employees.
As a philosophy, Kaizen is about building a culture where all employees are actively engaged in suggesting and implementing improvements to the company. In truly lean companies, it becomes a natural way of thinking for both managers and plant floor employees.’
In the IHI’s document ‘Comparing Lean and Quality Improvement’ the authors say: ’Detailed standardization of tasks refined via Kaizen means that ever smaller deviations in methods and quality can be discerned as problems, then quickly corrected, thus leading to ever greater consistency of product and conformance to specifications.’
The Kaizen cycle is all about identifying opportunities and issues, then creating solutions and implementing them. You can then go through the cycle again to check for any issues. The Plan-Do-Check-Act (PDCA) and Plan-Do-Study-Act (PDSA) provide the framework for Kaizen, enabling the user to identify improvement opportunities and evaluate them.
With the methodology of Kaizen being based on the principle that ‘everything can be improved, and nothing is the status quo,’ Kaizen also has an important ‘respect for people’ focus.
Let’s take a look at the Kaizen cycles, which are also known as the Plan-Do-Study-Act cycle or the Plan-Do-Check-Act
You can read more about PDSA and PDCA in our blog.
You can also find out more about Lean and Kaizen principles.
So, we’ve had a look at the types of models that are used in Kaizen, such as PDSA and PDCA and to apply the Kaizen model, you need to follow some very simple steps, along the lines of:
If you are thinking about applying Kaizen methodologies at your organisation, you can look at some examples where Kaizen has been implemented in healthcare organisations. There is a great example of where the Kaizen model has been applied in practice at the Western Sussex Hospitals NHS Foundation Trust where they established a ‘Kaizen Office’ and ‘aligned its workforce strategy with its QI approach using a patient-first concept and developed a capability-building programme to equip staff with the skills to deliver continuous improvement, with training available for every staff member.’
You might also want to think about using a software solution such as Life QI, which helps you to run, organise and measure all your improvement work in one place. You can then review your PDSAs all in one place and measure impact.
If you are thinking of using Kaizen at your organisation, it’s really important that you get buy in across the board, as ‘regardless of methodology, in an organizational setting, the successful use of Kaizen rests on gaining support for the approach across the organization and from the CEO down.’
Good luck in your continuous improvement journey!
Full access to all Life QI features and a support team excited to help you. Quality improvement has never been easier.
Organisation already using Life QI?
Sign-up