Start improving with Life QI today
Full access to all Life QI features and a support team excited to help you. Quality improvement has never been easier.
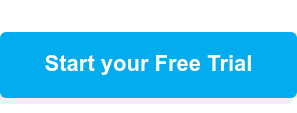
Organisation already using Life QI?
Sign-up
The PDSA cycle is a simple yet powerful method for encouraging a culture of continuous improvement. It's invaluable in healthcare but can be applied to almost any area where you want to see positive change.
But what is a PDSA cycle in quality improvement and what are its benefits? In this article, we will show you how it can be a useful tool for making improvements within your organisation through some examples from the healthcare industry.
You may well be familiar with the PDSA cycle, also known as Plan-Do-Study-Act cycle, which has its roots in the early 20th century.
Walter A. Shewhart, a physicist and statistician at Bell Laboratories, developed the Plan-Do-Check-Act’ (or PDCA) cycle in the 1920s as a method for statistical quality control.
Later, in the 1940s, W. Edwards Deming, a renowned quality management expert, further refined and promoted Shewhart's cycle, renaming it the Plan-Do-Study-Act (PDSA) cycle. Dr. Deming emphasised the PDSA Cycle with a third step emphasis on Study (S), not Check (C). He stressed the importance of not only implementing the results (whether they’re a success or a failure), but actually, studying them and learning from them.
He believed that organisations should constantly strive to improve their processes and products by systematically testing changes, analysing the results, and implementing the most effective solutions.
Read in more detail about the difference between PDCA and PDSA cycles.
The PDSA cycle is an iterative four-step model for improvement which is often used to provide a framework for quality improvement changes. The PDSA methodology encourages a systematic approach to testing changes, learning from the results, and refining the process.
Figure 1: PDSA cycle as part of the Model for Improvement
Based on scientific method, PDSA cycles were designed to effectuate positive change and provide a rapid way for teams to test out small changes and build on them. They also give stakeholders the opportunity to establish whether proposed changes will succeed. A powerful tool, the PDSA helps teams learn from ideas and establish what works and what doesn’t.
Think of it as a mini-experiment – a structured way to try out new ideas, assess their impact, and make informed decisions.
The PDSA model is a real ‘trial-and-learning’ method. It uses quality tools to identify problems, review causes and create solutions with the aim of continuous improvement. The aim of the process is to repeat until you implement a successful, sustainable improvement.
The first thing you need to do, however, is to identify what you want to achieve.
Figure 2: The 4 steps of the PDSA cycle
Let’s take a look at how to execute the PDSA cycle in more detail:
This is the stage when you agree on the change that will be tested and plan your actions for the cycle. You would also agree on and form a team that will be managing the process and who will be responsible for the PDSA cycle.
At this stage, you need to identify exactly what your objectives are and what you want to achieve. It’s also a good idea to work out what measurements you will use to measure your changes.
Key questions you should ask in this phase include:
So, in this step you have to:
This stage is the implementation phase when you will carry out the change or test. It may be a very small test, and we strongly encourage you to test one change at the same time. So, this is when the action takes place and when you will be observing where any problems lie and start collecting data for analysis.
In Life QI you can easily record all stages and collect data that you will review within the ‘Study’ phase.
Now comes the crucial part – analysing the data you collected in the ‘Do’ phase. It needs to happen based on the outcomes that you agreed on during the ‘Plan’ phase. Once you have collected the data, you can review, discuss and reflect with your team about the impact of the change and the test and about what you have learned.
Compare your results to your predictions, identify what worked and what didn't, and draw conclusions. Was your hypothesis correct? What did you learn?
Now is the time to agree what you need to tweak or whether you should abandon the test. Or indeed whether the results mean a positive outcome can be followed through going forward.
Read more about how to decide whether to adopt, adapt or abandon.
At this stage, you will be acting on the data that you have collected. This may help you to plan the next change cycle based on the reflection in the ‘Study’ phase. You may also be planning full implementation on a larger scale based on your results. You can use the results of one cycle to inform an enhanced idea to be tested in a new cycle.
Then – it’s back to the planning stage again to repeat the process!
Widely promoted and recommended by organisations such as the Institute for Healthcare Improvement (IHI), who use them within their Model for Improvement, PDSAs are used by a wide range of organisations for quality improvement, as they are a quick way of allowing your team to test out small changes.
PDSAs are also a key process within the Kaizen method - the basis of Lean methodology and a systematic approach for continuous improvement invented by Masaaki Imai.
PDSAs can really help to build an organisation-wide approach to improvement. So, if you want to make quality changes within your organisation, you should consider using the PDSA model to support this change! The step-by-step approach and cyclical process by which you measure and repeat, means PDSAs are ideal for many improvement projects. They also enable you to demonstrate that by making small changes, you can make big improvements.
Running PDSA cycles has many benefits for your organisation from continuous improvement to reduced risk and increased efficiency. You can learn more about the benefits of PDSA cycles in our dedicated blog article.
While there are many downloadable PDSA templates out there, nowadays many organisations use a QI platform such as Life QI, which gives teams better access to the data they need to understand quality and performance and to support their QI projects effectively.
A solution such as Life QI with an integrated PDSA tool means you can overview your whole project, understand where the PDSA cycle fits in the project by connecting your PDSA cycle to the Driver Diagram. You can also attach measures to your PDSA cycle and add your data to a run or SPC chart in the ‘Do’ phase which will be very handy in the ‘Study’ phase or in general for project reporting.
But that’s just the beginning. Life QI also allows you to ramp up your PDSA in case you need to adopt something in the ‘Act’ stage. Life QI connects these PDSA cycles together for a better overview of the changes.
Implementing a QI software also helps you to collaborate with team members quickly and easily and keep a record of changes, and see what other organisations are working on (if available) and what works well for them to get inspired.
More resources:
How to execute and learn from your PDSA cycle using Life QI
How to plan your PDSA cycle using Life QI (with examples)
The PDSA tool is immensely valuable also in the healthcare settings, often employed to improve patient care, streamline processes, and enhance patient safety.
If you decide to start looking at using PDSAs within your organisation, you may want to start small and build up. It’s worth looking at how other organisations have used PDSAs and the results they have had – and learning from others’ experiences.
We implemented the program on a small pilot group of patients on Ward A. We started with distributing printed materials and our nurses gave also verbal education to patients before their discharge. Our team also did follow-up calls to patients 3 days, 1 week and 2 weeks after the discharge to monitor them closely.
After analysing the readmission rates for the pilot group compared to historical data, we saw incredible results. Our readmission rate decreased significantly after implementing the changes. We also gathered and analysed feedback from patients on the program.
The program was successful, and we achieved the expected results, so we will expand it to all patients.
The nurses were well briefed about the test, so most patients were taken out of bed 3 times a day, but not all as there were operational/staffing pressures at a few points in the day that prevented it.
The results were broadly in line with expectation. Although staff were well briefed about the rationale and need for the change, we did not mitigate for the high-pressure points in the day which meant patients were not taken out of bed at those times.
As well as re-enforcing the communication with nurses, we will spend time planning for how we work the test around the inevitable pressure points of the day. If we succeed, we should be able to hit the 3 times a day target.
This PDSA was introduced as an addition to structured and planned activities. Over a period of three months additional and new activities were introduced. We noticed many of our patients really enjoyed being spontaneous and having the freedom to make choices and try new things at the times they felt most able. We noticed that there were still patients who struggled to engage in these activities, and we found that patients greatly valued increased contact with families.
Although we saw a slight reduction in number of seclusion episodes it was not as regular as hoped. The results were better early on when staff were conscious of the activity boxes and so encouraged service users to engage with them more than later in the test.
Adapt this PDSA to include more prioritisation of building of relationships and activities with family members. We will also expand the variety of options in the activity boxes to cater for a broader set of service user interests.
For more examples check out our How to plan your PDSA cycle using Life QI (with examples) blog article.
We hope that this will give you food for thought about using PDSAs in your organisation. It’s also worth bearing in mind, that building an organisation-wide approach to an improvement culture does takes time, however PDSAs can be an easy win for all!
So, embrace the PDSA cycle, and start your journey towards continuous improvement today!
Full access to all Life QI features and a support team excited to help you. Quality improvement has never been easier.
Organisation already using Life QI?
Sign-up