Start improving with Life QI today
Full access to all Life QI features and a support team excited to help you. Quality improvement has never been easier.
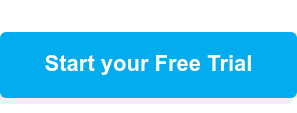
Organisation already using Life QI?
Sign-up
Published on 16 November 2022 at 13:57
Armand V. Feigenbaum – also known as the ‘Father of Total Quality Control’ - was born in 1922 in New York City. His life’s work has hugely influenced the thinking of Quality Improvement (QI), with his book ‘Quality Control: Principles, Practice, and Administration’ helping to bring together his ideas and principles on the theory of Total Quality Control (TQC). In this article, we’re going to find out more about his life, work and what inspired such pioneering quality work.
Armand V. Feigenbaum was born in New York City in 1922. He studied at Union College, receiving his master's degree from MIT Sloan School of Management and gaining a PHD from the Massachusetts Institute of Technology. Another pioneer from the General Electric Company stable, he started to work as an intern apprentice toolmaker in New York City when he was just 17 and rose to become Manager of Manufacturing Operations and Quality Control.
While working with Toshiba and Hitachi in the early 1950s, he visit Japan, where he taught on ‘customer satisfaction and results-driven quality’. He was in charge of production and quality control at the General Electric Company from 1958-1968.
He founded General Systems Company in Pittsfield MA 1968, where he was President and CEO. The General Systems Company was ‘a global leader in designing and installing proprietary management operating systems to accelerate the competitive business strengths for manufacturing and service companies throughout the world.’
As well as a busy career in quality, he was elected Vice President of the American Society for Quality from 1958 - 1961. Later he became the President of the American Society for Quality (1961 – 1963). In terms of recognition for his quality work, he obtained the National Medal of Technology and Innovation by President Bush in 2008.
Armand V. Feigenbaum wrote many books on quality management, with his 1951 book entitled ‘Quality Control: Principles, Practice, and Administration’ helping to bring together all his ideas and principles on the theory of Total Quality Control (TQC).
In terms of his influence on quality, he is often cited alongside improvement heroes such as Dr. W. Edwards Deming and Dr. Joseph Juran.
He died in 2014, having inspired generations of quality innovators.
Feigenbaum is famous as the father of ‘Total Quality Control (TQC)’, and for making the customer the heart and focus of TQM. The development of TQM saw him draw the focus away from the technical side of quality and drill down into what product might be ‘best for the customer’.
His inspiration for the creation of TQC happened when he was heading up Quality at General Electric, when he was influenced by – and learned from - quality work carried out by companies such as Toshiba and Hitachi. He studied their approaches to quality and thus came up with his “total approach to quality,’ to ensure the creation of high quality products.
He wrote his first book ‘Total Quality Control’ which was key to establishing the principles of TQM. This has gone on to influence people across the globe and is still available in print today. The premise of the book was: “Total quality control is an effective system for integrating the quality development, quality maintenance, and quality improvement efforts of the various groups in an organization so as to enable production and service at the most economical levels which allow full customer satisfaction.” The book has had several editions and has been printed in more than twenty languages.
Feigenbaum also invented the ‘hidden plant’ concept. The theory that up to 40% of the capacity of the plant is wasted each time something does not go right the first time.
Here are Dr Feigenbaum’s elements of total quality to lead to a total customer focus:
Feigenbaum and his brother Donald set up General Systems which enabled him to spread the TQM message to other organisations, so they could benefit from his theories.
As well as developing the concept of TQM, Feigenbaum developed the idea of the three steps to quality. He defined it as: leadership, modern quality technology, and an organisational commitment to quality. These are:
Management should take the lead in enforcing quality efforts. It should be based on sound planning.
The traditional quality programmes should be replaced by the latest quality technology for satisfying the customers in future.
Motivation and continuous training of the total work force tells about the organisational commitment towards the improvement of the quality of the product and the services.
It was here that his approach to quality slightly differed to those of another improvement hero, Deming. He felt that EVERYONE should be responsible of quality, not just the management alone. He approached quality ‘as a strategic business tool that requires awareness by everyone in the company’.
There is no doubt of the huge impact that Feigenbaum has had on the development of QI theories in healthcare.
“Total quality control is an effective system for integrating the quality development, quality maintenance and quality improvement efforts of the various groups in an organization so as to enable production and service at the most economical levels which allow full customer satisfaction.”
- Armand V. Feigenbaum
Full access to all Life QI features and a support team excited to help you. Quality improvement has never been easier.
Organisation already using Life QI?
Sign-up