Start improving with Life QI today
Full access to all Life QI features and a support team excited to help you. Quality improvement has never been easier.
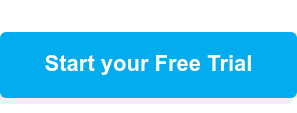
Organisation already using Life QI?
Sign-up
Published on 26 May 2022 at 10:44
Edwards William Deming (1900-1993) is considered by many to be the founder of the quality movement and a real reference in the field of statistics. Many in Japan also consider him to be one of the inspirations of the Japanese economic miracle, which occurred from 1950 to 1960. Japan grew from the ashes and became the second largest economy in the world, thanks to processes influenced by the ideas of Deming.
In this article, we’re going to focus on William Edwards Deming – more known commonly as W. Edwards Deming - his life and his contribution to improve statistical process control and total quality management (TQM).
He was born in Iowa in 1900 and was a leading management thinker, statistician and business consultant. Much of his work has paved the way for the Quality Improvement methods we use today.
His modest upbringing in rural Iowa contributed to his being interested in thriftiness and having a dislike of waste. Deming studied engineering at University of Wyoming, completed a Master’s in mathematics and physics at the University of Colorado and finished his studies at Yale University in 1928.
While studying, he also worked as a summer intern at the Western Electric Hawthorne factory complex in 1925 and 1926. This experience became a key influence on his future thinking. This is where he became interested in Walter A. Shewhart’s work and where he started to lay the foundations for his thinking and focus. After completing his studies, he spent the next 10 years lecturing and writing on mathematics, physics and statistics, before joining the US Census Bureau in 1939.
Edwards Deming became interested in – and a follower of – Walter A. Shewhart when they met while both working at the Western Electric Company Hawthorne factory in Illinois. There, he became familiar with Shewhart’s experiments on the application of statistical techniques to manufacturing processes, and he developed an interest in applying these theories to processes that were not yet associated with manufacturing. This led to him developing concepts and processes which would later be used in areas such as management and administration. Whilst teaching at Stanford, he shared the Shewhart Cycle for Learning and Improvement.
Walter Shewhart originally came up with the concept of the Plan-Do-Check-Act (PDCA) cycle and introduced it to Deming, who went on to promote it during the 1950s when it was originally known as the Deming Wheel or the Deming cycle.
Along with Joseph Juran, - who also worked at the Hawthorne factory complex from 1924 to 1941 - Deming and Shewhart and are often cited as the three founders of the quality improvement movement.
When he joined the US Census Bureau in 1939, Deming started to apply statistical process control (SPC) to the techniques used there, which led to a six-fold improvement in productivity. As he evolved and grew his methods of statistical process control, he also started to run courses for designers and engineers in industries involved in the war production efforts to understand variation and statistical process control.
He also helped share the PDCA (Plan-Do-Check-Act) cycle which resulted in improved quality of wartime production. Although the original creator of the PDCA cycle was Walter A. Shewhart. Edwards Deming promoted its use for process improvement and later changed it to the PDSA cycle (Plan-Do-Study-Act).
‘Both methodologies are widely used for problem-solving and to create quality process improvements. Both methods also use a step-by-step approach and cyclical processes which measure, repeat and are ideal for many improvement projects. They can both help to build an organisation-wide approach to improvement via changes in culture’.
After the World War 2, with his reputation as a statistician growing - but not receiving the recognition he necessarily merited in the US - Deming was posted to Japan to advise on the Japanese Census. Not only did his work help to speed up Japan’s recovery after the war, but it was here that he developed what is now known as ‘Total Quality Management’ (TQM).
Deming’s work influenced the creation of Total Quality Management (TQM), a technique that focuses on continuous improvement and quality. Defined by ASQ as ‘A management approach to long-term success through customer satisfaction. In a TQM effort, all members of an organization participate in improving processes, products, services, and the culture in which they work.’
By developing TQM, Deming created a method that encouraged organisations to plan, in order to continually improve themselves, along with their processes, products and services. The philosophy of TQM is one of ‘cooperation and continual improvement; it avoids blame and redefines mistakes as opportunities for improvement.’
Due to Deming’s work in Japan, TQM became popular in Japan 30 years earlier than in the United States, which would go on to be pivotal in the success of Japanese manufacturing.
An ambassador for Quality Improvement – his theories simple, but radical - Deming’s approach to quality promoted the following theory. ‘Organizations that focused on improving quality would automatically reduce costs while those that focused on reducing cost would automatically reduce quality and actually increase costs as a result.’ Deming outlined his ideas simply in his theory of management, now known as The System of Profound Knowledge (SoPK), which is now seen as the culmination of his lifelong work.
The ELFT QI team describe The System of Profound Knowledge as ‘An effective theory of management that provides a framework of thought and action for any leader wishing to transform and create a thriving organisation, with the aim for everybody to win. By management appropriately applying the principles and practices of SoPK, a business can simultaneously reduce costs through reducing waste, rework, staff attrition and litigation, while increasing quality, customer loyalty, worker satisfaction and, ultimately, profitability. SoPK ties together Dr. Deming’s seminal theories and teachings on quality, management and leadership into four interrelated areas: appreciation for a system, knowledge of variation, theory of knowledge and psychology.’
You might want to take a look at this really interesting video from the QI team at ELFT about the System of Profound Knowledge. In this video Robert Lloyd, Vice President at the Institute for Healthcare Improvement talks through this theory.
“It is not enough to do your best; you must know what to do and then do your best.”
- William Edwards Deming
Full access to all Life QI features and a support team excited to help you. Quality improvement has never been easier.
Organisation already using Life QI?
Sign-up