Start improving with Life QI today
Full access to all Life QI features and a support team excited to help you. Quality improvement has never been easier.
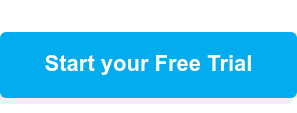
Organisation already using Life QI?
Sign-up
Published on 10 August 2022 at 11:48
In this article, we are going to look at Joseph Juran’s career in quality management, and look at the ground breaking work he pioneered in quality control. His theories and techniques have filtered down to Quality Improvement (QI) work today. Primarily his Juran Trilogy and the important quality work he did in both the USA and Japan.
Dr. Joseph Juran was born in Romania in 1904 and emigrated to Minnesota in the US with his family in 1912. He achieved a bachelor's degree in electrical engineering from the University of Minnesota and in 1924 he went to work at Western Electric’s Hawthorne Works in the Complaint department. At Hawthorne Works he began to learn about quality control techniques and he started to work on statistical sampling.
You may remember from previous blogs that both Walter A. Shewhart and W Edwards Deming also worked at Hawthorne Works during the 1920s, where Deming went on to champion Shewhart's methods. Joseph Juran also worked at Hawthorne Works from 1924 to 1941. So, it's not a surprise that Shewhart and the pioneering work going on there at the time influenced his work.
Juran went on to teach quality control at New York University after the second world war and it was during this time that his work attracted attention in Japan. He went to Japan initially in 1954 in order to discuss his techniques and theories, and would continue to visit on a regular basis - a further nine times - teaching his theories which were adopted by the Japanese manufacturing and engineering industries.
Dr. Joseph Juran founded the Juran Institute in 1979 with a mission to “create a global community of practice to empower organizations and people to push beyond their limits”. The foundation is still going strong today, leading change and creating capability for organisations across the globe.
In 1941, Juran came across the work of economist Vilfredo Pareto. In particular, the Pareto Principle, also known as the 80/20 rule. ‘It follows the observations of Vilfredo Pareto, whose studies showed that 80% of the land in Italy was owned by 20% of the population.’
Juran started applying the Pareto Principle to quality issues. He came up with the phrase: “the vital few and the trivial many” to demonstrate that a small percentage of causes can lead to a higher percentage of issues. ‘In later years, Juran preferred "the vital few and the useful many" to signal that the remaining 80% of the causes should not be totally ignored.’
Juran introduced the Juran Trilogy – or Quality Trilogy - in the late 1980s. This was a new way of thinking about quality, and also a way of managing quality. And is now the basis for much quality management work.
Source: www.juran.com
These are the three components of the Juran Trilogy:
This is a structured method that relates to product or service development processes and is used in order to create new features that customers actually need. You may also know it as the ‘Design for Six Sigma’.
This is a focus on ‘breakthrough’ improvement, rather than everyday improvement. ‘By attaining just a few vital breakthroughs year after year (The Pareto Principle), the organization can outperform its competitors and meet stakeholder needs.’
‘Today, the term “quality control” often means quality control and compliance. The goal is to comply with international standards.’
Although the Juran Trilogy has evolved over the years, it ‘continues to be the means to present total quality management to all employees looking to find a way to keep it simple.’
Juran also created, designed and advocated a ten-step process for quality improvement programmes:
You can also read more about each step in the ‘Juran’s steps for Quality Improvement’ article. It goes into further details for each step of the programme.
You will recognise that these improvement steps – and the associated detail – from QI work today.
As we know, many talented quality management pioneers transferred their knowledge from East to West and West to East. Dr Juran had many visits to Japan to share his knowledge.
As we have explored in previous articles about Shewhart and Ohno – theories and techniques were transferred across the world, meaning that Juran’s quality improvements steps have been practiced over time to suit different sectors.
An interesting element of the theories - which were popular in Juran’s early days in quality management - was the focus on the quality of the end product. It was something that Deming was particularly interested in.
However, Juran changed all this when he shifted the focus away from the end product and onto Quality Management’s human element and with this – a focus on how vital it was to train and educate managers.
Juran recognised that resistance to change was a real problem in achieving true quality management. So, he was trying to address this balance during his pioneering work. He recognised that the management had to be responsible for focusing on quality issues and setting associated goals.
“Without a standard there is no logical basis for making a decision or taking action.”
- Joseph Juran
Full access to all Life QI features and a support team excited to help you. Quality improvement has never been easier.
Organisation already using Life QI?
Sign-up