Start improving with Life QI today
Full access to all Life QI features and a support team excited to help you. Quality improvement has never been easier.
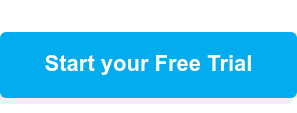
Organisation already using Life QI?
Sign-up
Published on 10 October 2022 at 12:09
Kaoru Ishikawa is considered the ‘Father of Japanese Quality’ for his creation of innovative developments in quality management. He is famous for creating the fishbone diagram, a type of ‘root cause analysis’ which we still use in Quality Improvement (QI) to help make decisions and create actions. Ishikawa is a hugely respected figure in Quality Improvement, having been instrumental in developing quality initiatives in Japan.
Kaoru Ishikawa was born in Japan 1915. He studied at the University of Tokyo, and in 1939, he obtained his Master’s degree in applied chemistry and obtained his doctorate from the university in 1960. Kaoru Ishikawa served in the Japanese Navy from 1939-1941, thereafter joining the Nissan Liquid Fuel Company.
He returned to science in 1947 when he started working as a professor at the University of Tokyo. In 1949 Kaoru joined a quality control research group, the Japanese Union of Scientists and Engineers’ (JUSE). In 1954, he wrote 'Introduction to Quality Control' – and went on to write many other books during his distinguished quality career.
Known as the Father of Japanese Quality because of the many concepts and quality tools that he designed, in 1945, Kaoru Ishikawa developed and presented the first iteration and concept of the ‘fishbone diagram’ a ‘problem solving model helps determine root causes of problems.’
This is also known as the cause and effect diagram and is often used while analysing industrial processes. He also created the concept of Company Wide Quality Control and the concept as the putting the client front and centre of the manufacturing process.
Kaoru Ishikawa became a member of ISO, Japan in 1969 and in 1981 he published ‘What is Total Quality Control? The Japanese Way’. He died in 1989, leaving behind a valuable legacy in QI.
When the industrial sector changed after the Second World War in Japan, Kaoru Ishikawa met Deming and Juran. They worked together to develop management concepts that are still in use.
Ishikawa invented the concept of ‘quality circles’ in 1960. Quality circles are groups of people who meet to improve organisational performance. Although the only company to take part in the original ‘quality circles’ study was Nippon Telephone and Telegraph, the study was a great success and went on to gain traction and become more and more popular as part of the concept of Total Quality management (TQM). Ishikawa also created the concept of ‘Internal Customers’ highlighting how important employees are to any organisation.
Kaoru Ishikawa had such a key influence in process improvement and quality control with his Fishbone diagram still used across the globe today to understand the causes of quality gaps and how these gaps effect the organisation’s function.
Ishikawa had a huge input into the development of Total Quality Management and to Process improvement Methodologies. He had a strong belief that you should service your customers even after they have bought your organisation’s products.
Ishikawa was also instrumental in creating processes to address customers’ needs which led to better quality and process efficiency. He came up with the policy of “the next process is your customer,” which encourages better cooperation within a company.
Ishikawa also promoted the fact that high level personnel should be able to support their teams at all times and was a firm believer that they should take quality control courses.
The Fishbone diagram - also known as the Ishikawa diagram and the cause and effect diagram - was developed and created by Ishikawa and was originally used to analyse the cause of problems within quality management. It's called Fishbone Diagram due its shape – the head stating the ‘problem’, and the bones showing the various causes. It is known as one of the seven quality control tools.
Let’s have a look at how the Fishbone Diagram is used today in QI in healthcare. The QI team at East London Hospital Foundation Trust describe it thus: ‘The ‘effect’ is the problem you are working on, for example ‘waiting time’.
The tool can help you identify major causes and indicate the most fruitful areas for further investigation. It will help you understand the problem more clearly. By going through the process of building the diagram with colleagues, everybody gains insights into the problem, alongside possible solutions.
The people involved benefit from shared contributions, leading to a common understanding of the problem.’
You can read more about the team’s recommendations and how you can use the diagram to ‘enables a team to focus on the content of the problem rather than its history or the differing interests of team members.’
Ishikawa also invented the concept of quality circles in 1960. Quality Circles are groups of people who meet voluntarily to improve organisational performance. Or they're ‘formal groups of people trained by specialists in human factors and skills of problem identification, data gathering, and analysis and generation of solutions.’
When Ishikawa started to work on the concept, the only company to take part in the original study was Nippon Telephone and Telegraph. The study went on to be a great success and gained traction, becoming more and more popular as part of the concept of Total Quality management (TQM).
Once again, we can trace the thinking and the influence of W Edwards Deming to Ishikawa’s quality management concept. Quality Circles were first described by Deming in the 1950s and the concept was expanded by Ishikawa.
“Think of at least four factors which influence your problem. See if a shift in one of these causes can give you a different effect to explore.”
- Kaoru Ishikawa
Full access to all Life QI features and a support team excited to help you. Quality improvement has never been easier.
Organisation already using Life QI?
Sign-up