Start improving with Life QI today
Full access to all Life QI features and a support team excited to help you. Quality improvement has never been easier.
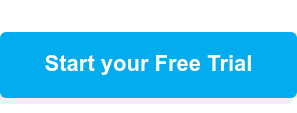
Organisation already using Life QI?
Sign-up
In this blog, we are going to be finding out more about Six Sigma - an improvement methodology created by Bill Smith, who is sometimes known as the ‘father of Six Sigma.’ Along with some colleagues, Bill Smith developed the methodology when he was at Motorola in the 1980s, based on Japanese quality methods that he had learned. This systematic approach to improvement focuses on reducing variance and eliminating defects and at its heart is the belief that in order to improve processes, you should involve people who are already doing the job.
In recent years, the Six Sigma approach is sometimes combined with elements of the Lean method, and referred to as Lean Six Sigma. The processes are complimentary, as where Six Sigma focusses on eliminating defects and reducing variation, Lean is focused on improving flow and eliminating waste.
Essentially, Six Sigma is a problem-solving approach to describe an ‘expected level of design margin and product quality’ and has four stages, as follows:
This approach was originally known as MAIC, which later became DMAIC – more on that later.
There are a wide range of tools and methods that can be used that build on the key principles of Six Sigma, which are:
Let’s drill down into the details, starting with Six Sigma DMAIC and Six Sigma DMADV.
Fundamental to improvement with Six Sigma is the DMAIC (Define, Measure, Analyse, Improve and Control) framework.
DMAIC is a five-phased data-driven method for improving, optimising or stabilising existing processes. Whilst it is a key tool within the Six Sigma methodology, it is also widely implemented on its own. The DMAIC framework lies as the heart of Six Sigma and provides a step-by-step approach to achieving sustained improvement.
Let’s take a look:
The first step is to clearly define the problem to be solved and get a clear understanding of the process in its current state. Typically, a project charter is initiated which includes a problem statement, business case, goal statement, timeline and scope.
Here, metrics are chosen to accurately assess the current state of a process and to quantify future improvements. This includes choosing appropriate measures and collecting a baseline dataset to which the results of any improvement effort can be compared.
The data collected in the measure phase are examined to determine the root cause of the problem and identify areas for improvement.
The learning from the previous three phases is applied here to determine how the process could be improved. These solutions are tested to ensure they deliver the desired results. Successful solutions may then be implemented.
This is where steps are taken to ensure successful improvements are sustained over time and don’t revert back to the ‘old way’. This includes continued monitoring of key measures and the embedding of the improvements through the modification of systems (like documentation or training).
This method is applied to processes already in existence.
While DMADV stands for:
The DMADV methodology is used to create a new process and adds two new steps: Design and Validate. The Design step involves creating a detailed design for a new model, which is created to find out where any errors may occur and how these can be tweaked.
During the final step, Validate, the team validate whether the design is acceptable to all, it might be a time to pilot the model and all learnings will be documented. This is also the time to develop a control plan to ensure that any changes meet customer specifications.
Invented by Kaoru Ishikawa the ‘Father of Japanese Quality,’ he created the first iteration and concept of the ‘fishbone diagram’, also known as the ‘cause and effect diagram’.
This diagram is often used to analyse industrial processes and is a type of ‘root cause analysis’ used to help make decisions and create associated actions.
The IHI recommends that you use the fishbone diagram to: ‘show causes of problems at each step in the process.
A cause and effect diagram has a variety of benefits:
The NHS Institute for Innovation and Improvement's document 'Lean Six Sigma: some basic concepts' cites SIPOC as a type of Six Sigma tool. It is an acronym for: Stakeholders, Inputs, Process, Outputs, and Customers.
In ‘Advanced Quality Management: Learn about QI Tools You Might Not Have Ever Used Before’ the report advises when to use the tool:
In the NHS Institute for Innovation and Improvement's ‘Improvement Leaders’ Guide Process mapping, analysis and redesign’ it states: ‘Process mapping is a simple exercise in your toolkit of improvement methods. It helps a team to know where to start making improvements that will have the biggest impact for patients and staff. The ‘Model for Improvement’ helps a team to set aims, targets and measures, and introduces a way of testing ideas before implementing them. So it’s logical to consider the two together.’
The report ‘Advanced Quality Management: Learn about QI Tools You Might Not Have Ever Used Before’ describes process mapping as a method to help describe a process visually to:
There are several tools for mapping a process:
The end goal of every Six Sigma process is ‘near perfection in a process’. Six Sigma puts a real focus on understanding the true cause of a problem and focussing improvement effort where most impact can be made.
Six Sigma’s zero tolerance for mistakes mean it is well suited for healthcare improvement, particularly true in improvement focussed on minimising medical errors. As so much effort is put into the preparation part of the process, DMAIC is perfect for large or complex improvement projects that come with big risks or will be expensive to implement.
However, the approach is sometimes criticised for being too rigid in nature, therefore limiting the scope of projects to which it can be applied and making it slow to recognise improvements. Whilst big focus is put on understanding the problem, the Six Sigma process is largely linear, particularly when compared to other techniques such as PDSA, which aim for incremental change.
Typically, Six Sigma is used by organisations where the methodology is formally incorporated, directed by highly trained certified individuals (using a martial arts derived belt grading approach), and is less applicable on an ad-hoc basis.
It is for this reason that it is sometimes combined with elements of the Lean methodology in a hybrid, Lean Six Sigma approach, which may be approach to explore when you are considering which methodology to use in your organisation.
Full access to all Life QI features and a support team excited to help you. Quality improvement has never been easier.
Organisation already using Life QI?
Sign-up