Start improving with Life QI today
Full access to all Life QI features and a support team excited to help you. Quality improvement has never been easier.
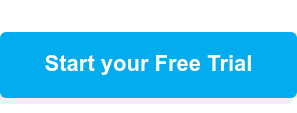
Organisation already using Life QI?
Sign-up
Lean is a quality management system with a focus on improving flow and removing ‘waste’ from a system or process and making it as efficient and effective as possible for the customer. Driven by the identification of customer needs, Lean maximises value for the customer and aims to improve processes by removing activities that are non-value-added.
In Lean, waste is any action or step in a process that does not add value to the customer. Essentially, Lean is all about doing more with less and cutting out anything that is unnecessary!
The concept behind Lean originated at Toyota in Japan in the 1950s, with the development of the Toyota Production System, created by Taiichi Ohno. You can read more about Ohno’s work in our ‘Quality Improvement heroes’ series.
The success that was demonstrated by the Toyota Production System led to the technique being adopted by other manufacturers, and the widespread application of similar tools and techniques to other industries, in the 1990s. This is when the approach started to become known as ‘Lean’.
Lean methods are often used in combination with Six Sigma, in a process called ‘Lean Six Sigma’. Lean and Six Sigma are considered complimentary techniques, as Lean deals with eliminating waste from a process, while Six Sigma focuses on reducing the rate of defects in the output.
Many organisations have adapted the Lean approach to address specific industry goals. In healthcare, one of the most well-known examples is the Virginia Mason Production System, which has been applied in numerous healthcare organisations with great results.
Let’s have a closer look at the set of principles which form the core of ‘Lean’.
Value should always be considered from the customers perspective - in healthcare this is normally the patient! The start of the process is to determine what it is important to the customer.
This is where the value defined and used as a reference point to identify all related activities. Any steps in the process that do not contribute to that value are considered waste and should be eliminated or minimized.
Value creating steps should occur in a tight sequence so that the process runs effectively and flows continuously.
This ensures that customers are driving or ‘pulling’ demand on the system and that this is tracked back through the entire process. This avoids work or supplies being ‘pushed’ to the next process or department.
This is the iterative element to Lean – once all the previous steps are completed it is important to go back through the process until a state of perfection is reached.
The world of Lean is full of expressions from the Japanese origins of Lean, such as Muda (waste), Kaizen (continuous development) and Kanban (signboard).
Some improvement tools are fundamental to the Lean improvement approach, and are often just referred to as ‘Lean tools’. Each tool is designed to address the improvement of flow or the elimination of waste.
Some of the most commonly used Lean tools include Value Stream Mapping, A3 Diagrams, PDCA, Kanban Boards, 5s, 5 Whys and Ishikawa (Fishbone) diagrams. Whilst many of these tools have their origins in Lean, over time some of the tools have been more regularly incorporated into projects run using different methodologies, for example, the Model for Improvement.
Let’s take a closer look at some of the tools used within Lean:
ASQ has this to say about the 5S quality tool: ‘The 5S quality tool is derived from five Japanese terms beginning with the letter ‘S’ used to create a workplace suited for visual control and lean production. The pillars of 5S are simple to learn and important to implement:
Seiri: To separate needed tools, parts, and instructions from unneeded materials and to remove the unneeded ones.
Seiton: To neatly arrange and identify parts and tools for ease of use.
Seiso: To conduct a clean up campaign.
Seiketsu: To conduct seiri, seiton, and seiso daily to maintain a workplace in perfect condition.
Shitsuke: To form the habit of always following the first four Ss’.
Value stream mapping is a key Lean tool which is used to help set out and visualise exact steps in a process which will bring the organisation closer to its goal. ‘It is a visual representation of the flow of people, material, and information in a complex system. By including material and information, value stream mapping differs from a traditional process flow map.’
According to the Kaizen Institute , Kaizen is ‘an important pillar of an organisation’s long-term competitive strategy’ and ‘a systematic approach for business improvement’.
Kaizen is a compound of two Japanese words that together translate as "good change" or "improvement." Kaizen has its origins in post-World War II Japanese quality circles and - through its association with lean methodology and principles - Kaizen has come to mean continuous improvement. ‘Eliminating waste in the value stream is the goal of Kaizen. The PDCA (or PDSA) Cycle is the Lean working structure –the system for executing Kaizen.’
If you want to find out more about PDSAs, take a look at our blog.
The 5 Whys can be described as a ‘basic root cause analysis technique’ and it is used in the ‘Analyze’ phase of the Six Sigma DMAIC (Define, Measure, Analyze, Improve, Control).
The whole premise is that in order to solve a problem, the root cause needs to be identified and then eliminated. The 5 Whys helps you to drill down to the root of a problem to find out the cause and thereby prevent its recurrence.
Lean offers a structured way of thinking about and delivering improvement. Essentially, it is a focus on the customer or patient and all about developing a real understanding of what value means to them. Lean is very adaptable in terms of the types and scale of problems to which it can be applied – this is partly due to the fact that is it more of a way of thinking, rather than a project-by-project approach.
The terms “Lean thinking” and “Lean culture” are in common usage today and organisations who are most successful in using Lean have instilled the approach and culture across the organisation.
However, some people might argue that Lean may not be quantitative enough due to the fact that many of the core tools, like Value Stream Maps are qualitative in nature. This is in contract to other improvement approaches like The Model for Improvement or Six Sigma where much of the process is structured around quantification and measurement.
The tools and terminology in the Lean process are numerous and varied which can be off-putting at first, however this variety really just speaks to the adaptability of the process to different problems.
To summarise, with its focus on reducing waste and improving flow, Lean offers valuable methods to improve any system. However, this focus could in some cases be at the detriment of reducing variability and errors – this is one of the reasons Lean is often combined with Six Sigma methodologies.
Full access to all Life QI features and a support team excited to help you. Quality improvement has never been easier.
Organisation already using Life QI?
Sign-up