Start improving with Life QI today
Full access to all Life QI features and a support team excited to help you. Quality improvement has never been easier.
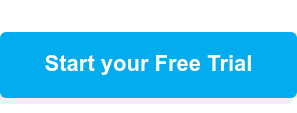
Organisation already using Life QI?
Sign-up
Over the course of this series of blogs, we’ve been looking at a wide range of improvement methods. You may have already decided which method you might be thinking of using in your organisation. Or, you may have identified something in your department that is either inefficient, or not quite right.
If this is a simple issue, with an obvious solution that you can control, you might just go ahead and make a change, knowing that improvement will follow. However, most issues might be more challenging and complex, with a number of driving forces and a need to work across teams or disciplines.
This is where you might choose to implement Quality Improvement (QI) methodology to help you.
When investigating improvement methods and looking at which one to use, it is important to look at the situation holistically.
Sustaining and scaling improvement in an organisation requires a holistic outlook, as improvement is most effective when it becomes part of everyday life and therefore central to the core values of an organisation. This is often referred to as a ‘culture of continuous improvement’.
You can run improvement projects which have a positive effect on outcomes. But if the approach is not embraced by the whole organisation they are unlikely to be sustainable.
If you are considering how you can build a culture of improvement within your organisation and which improvement method you should use, read on!
Let’s take a look at the most popular types of programmes available, which depend on the type and scale of the quality issue. Each of the main improvement methods strive for sustained change through defining clear goals, using structured processes and maximising the use of data.
Model for Improvement (MfI) – a cyclical improvement process using the well-known PDSA cycle, widely used in healthcare by many leading organisations.
Lean – a method for streamlining processes to deliver maximum value to the ‘customer’ or patient.
Six Sigma – a data-driven approach that strives to eliminate (or at least significantly decrease) variation and defects.
As these improvement methods have common underlying philosophies and methodologies, these approaches are not always used mutually exclusively. For example, elements of Lean and Six Sigma are often combined into the hybrid approach of Lean Six Sigma.
Different improvement methods have very different settings origins: from Japanese car factories to American telecommunications organisations; from consultants to innovators. These methods have differences in approach and application, normally stemming from the differing focus of the methods.
Having said that, these quality methodologies also have much in common. All models arise from pragmatic philosophies, are based on scientific method and have been proven to deliver continuous and sustained improvements in multiple settings.
Here are some of the common characteristics:
The tools used in different QI methodologies are generally not exclusive to the method followed. Although some tools are synonymous with particular methods, for example, Kaizen is synonymous with Lean.
Model for Improvement (or MfI) puts the PDSA cycle at the centre of its approach. Tools such as the Key Driver Diagram are also popular in this methodology.
Lean uses a range of different tools and methods for different situations. As the focus is improving flow, Value Stream Maps are fundamental to most Lean initiatives.
Six Sigma has a strong focus on root cause analysis, tools such as Pareto Charts and 5-Whys are common.
All methods use measurement tools, including Statistical Process Control (SPC).
The choice of which improvement method to use can sometimes be divisive. One single method is not necessarily better than another, with their strengths lying in different areas. That said, if you are thinking about finding an approach most suited to an issue you are hoping to resolve, these guidelines may help your decision-making process.
The Model for Improvement could be a good choice when a process or system needs changing, or if you need to introduce a new one. Using PDSAs to carry out small tests of change, the process is iterative and incremental. Scalable and simple for anyone to apply, the Model for Improvement makes it easier to see the results of change and increase confidence in effectiveness.
Lean could be a good choice if systems are inefficient, wasteful or flow poorly. It is particularly suitable for projects where flow/throughput is sub-optimal, leading to lower than planned output or poor experience. Lean cycles can be rapid, or long term and can vary in complexity.
Six Sigma could work well if there are obvious inconsistencies in quality and zero-tolerance to mistakes is required. The process can be long, but the results can be excellent. Unlike other methods, Six Sigma does not encourage incremental improvements but focusses on getting it right once.
For all of these methods, a Quality Improvement software can really help organisations in their planning, review and execution of QI work. Solutions such as Life QI enables users to keep all their QI work in one place, review, monitor and share with others, in order to spread learning.
To summarise, there are several different improvement methodologies that you could choose for your QI project or to make changes. While each method has its own merits, we wouldn’t want to recommend one approach over the other.
However, by drilling down into the detail of these methods, we hope it will make it easier for you to decide what will work best for you and your organisation!
Full access to all Life QI features and a support team excited to help you. Quality improvement has never been easier.
Organisation already using Life QI?
Sign-up